La méthode Lean et son concept de base des gaspillages (activités sans valeur ajoutée) ne peut pas seulement être appliquée à des organisations industrielles, mais aussi à des fournisseurs de services (Lean Office). Cependant, une application directe des gaspillages « classiques » est difficile, car il existe des différences fondamentales entre la fabrication d’un produit et la prestation d’un service.
Les gaspillages administratifs présentés dans cet article tiennent compte de ces particularités et permettent d’identifier plus facilement les inefficiences d’un service. Combinés avec la méthode Service Blueprint, ils permettent l’analyse complète et transparente de l’organisation liée à une prestation d’un service.
Table des matières
Distinction entre produits et services
Dans une organisation industrielle, les étapes de fabrication d’un produit sont définies en détail dans des gammes opératoires et des nomenclatures. Des inefficiences au niveau de la performance et de la qualité sont ainsi faciles à détecter et à mesurer. Dans le cas d’une prestation d’un service, la mesure des inefficiences est plus difficile à réaliser. En effet, selon le paradigme IHIP (Intangibilité, Hétérogénéité, Instantanéité et Périssabilité), il existe les différences suivantes entre un service et un produit (Regan) :
Intangibilité : Les services ne peuvent pas être stockés, et il est impossible de les voir ou de les toucher;
Hétérogénéité : Les services sont difficiles à standardiser, car ils dépendent souvent de la demande (imprévisible) du client;
Instantanéité : L’interaction entre le fournisseur d’un service et le client, qui se déroule en général d’une manière instantanée, influence le déroulement du service;
Périssabilité : Les services ne se gardent pas, et ils ne peuvent pas être retournés ou revendus.
Ces caractéristiques de services montrent donc qu’il est difficile d’utiliser les gaspillages classiques comme la Surproduction ou les Stocks inutiles pour identifier des inefficiences dans un processus administratif.
Définition d’une organisation optimale
Pour identifier les inefficiences d’un service, les gaspillages Attendre et Erreurs peuvent être appliqués sans problèmes. Dans le cas des autres gaspillages, l’application directe est moins évidente (Stocks inutiles, Transports, etc.). Pour définir des gaspillages administratifs adéquats, il est proposé de les déduire à partir des caractéristiques d’une organisation optimale. Toute activité en opposition à une telle organisation « optimale » peut donc être considérée comme un gaspillage administratif, car elle empêche le déroulement optimal d’une prestation de service.
Il existe un grand nombre de publications et livres sur le sujet d’organisations et services et il est ainsi possible de définir un certain nombre de caractéristiques, qui correspondent à un certain consensus au niveau de la définition d’une organisation optimale :
Organisation en accord avec des objectifs transparents et réalistes : Les objectifs sont transparents et réalistes et peuvent être atteints avec l’organisation en place et les moyens à disposition;
Fonctions et hiérarchies adéquates : L’organisation est caractérisée par une hiérarchie simple avec un nombre minimal de niveaux. Les unités d’organisation regroupent d’une manière adéquate et logique les fonctions et responsabilités;
Coordination et communication parfaite : La coordination et communication parfaite entre les unités de l’organisation favorise le partage de toutes les informations importantes;
Utilisation adéquate des ressources : Les ressources (collaborateurs-trices et unités d’organisation) sont utilisées selon leurs compétences et capacités et elles ont les moyens à disposition pour atteindre les objectifs;
Règles et standards adéquats et appliqués : Il existe des règles et standards permettant d’optimiser la performance de l’organisation et des méthodes d’analyse structurées sont appliquées pour résoudre les éventuels problèmes;
Satisfaction des collaborateurs-trices : Le cadre de travail est agréable et facilite la réalisation des objectifs;
Outils (IT) adéquats : Les outils (IT) à disposition sont simples à utiliser et ils facilitent la réalisation des tâches;
Travail d’équipe : Le travail d’équipe est favorisé pour traiter des problèmes complexes.
Les gaspillages administratifs
Les gaspillages administratifs suivants correspondent à des activités ou des formes d’organisation, qui caractérisent ou qui causent des inefficiences au niveau de la prestation d’un service.
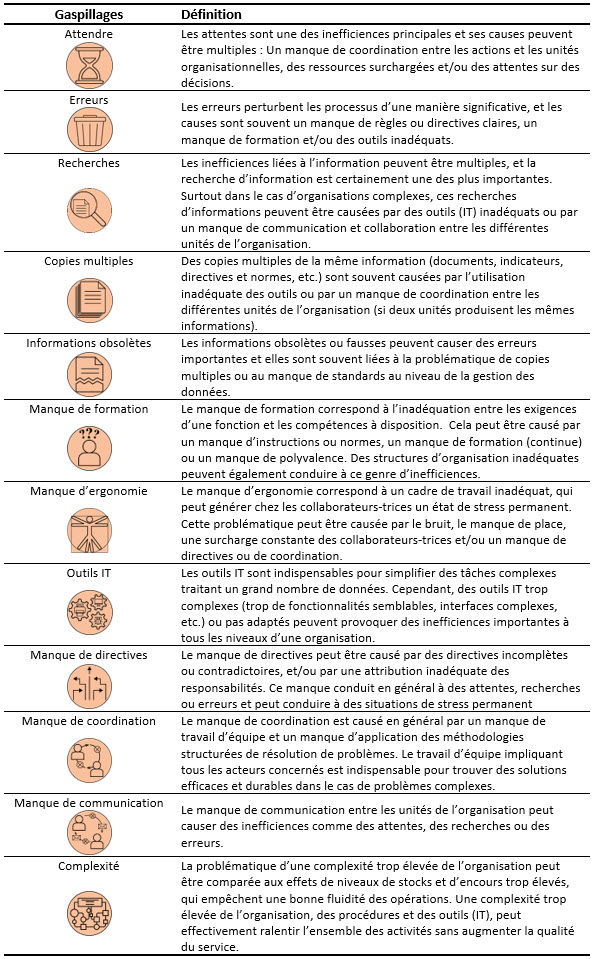
Application
Les gaspillages administratifs sont l’outil idéal pour identifier et classifier les inefficiences. Mais pour les placer dans le contexte d’une organisation, il est conseillé de les utiliser ensemble avec la méthode Service Blueprint. Le Service Blueprint est une représentation visuelle de tous les éléments d’un service et permet ainsi l’identification d’opportunités d’amélioration éventuelles.
La figure suivante illustre un exemple fictif d’un Service Blueprint couplé à l’identification des gaspillages administratifs.
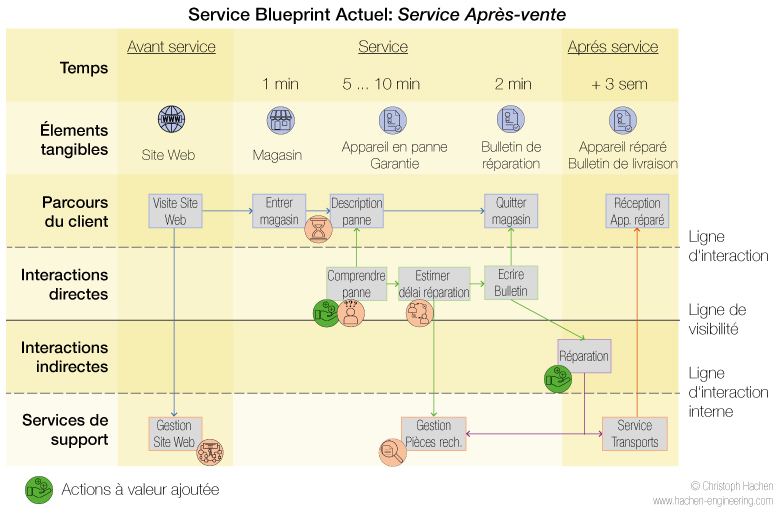
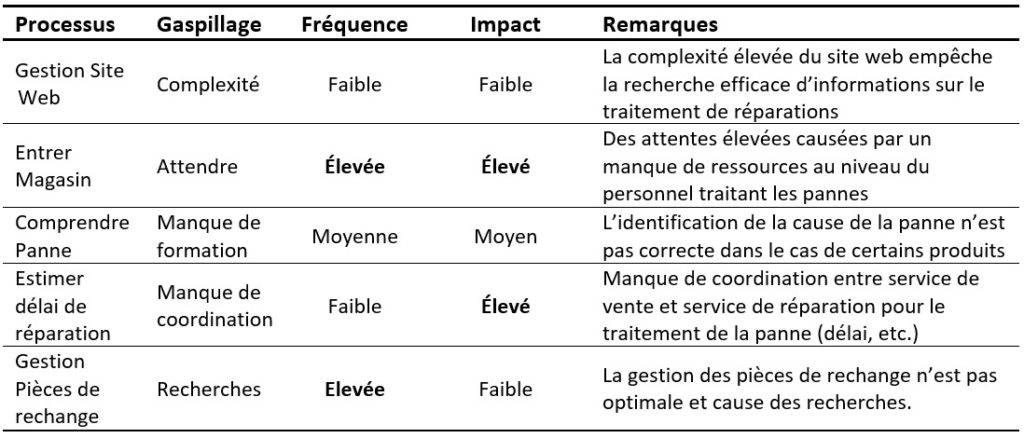
Résumé et questions fréquentes
Les gaspillages administratifs et le Service Blueprint sont des outils adéquats pour l’identification simple et transparentes des inefficiences d’un service. Ils simplifient également la recherche des actions correctives, car ils assurent une analyse globale de tous les éléments d’un service.
Contactez-nous si vous avez besoin d’une analyse détaillée de votre organisation ou service.
Question fréquentes:
Le concept de base des activités sans valeur ajoutée (gaspillages) reste le même. Mais comme il y a des différences significatives entre un produit et un service, il est nécessaire de faire quelques ajustements.
La différence principale entre un service et un produit est qu’un service ne peut pas être stocké (intangibilité). En plus, les services sont difficiles à standardiser, car ils dépendent souvent de la demande (souvent imprévisible) du client.
Les gaspillages « classiques » Attendre et Erreurs s’appliquent également à des processus administratifs. A côté de ces inefficiences typiques s’ajoutent la gestion insuffisante de l’information, le manque de coordination entre les unités d’organisation et des outils (IT) trop complexes ou inadéquats.
Les gaspillages administratifs permettent l’identification et la classification des inefficiences, et le Service Blueprint permet de les mettre dans le contexte de tous les éléments d’un service.
Le Value Stream Mapping est focalisé sur le flux de produits (et d’informations) dicté par des gammes de production (temps de passage, niveaux de stocks, etc.). Dans le cas d’un Service Blueprint, l’analyse est plutôt focalisé sur le parcours client (customer journey) et les interactions entre les différentes éléments d’un service.
L’analyse de risques est réalisée en attribuant à chaque gaspillage administratif sa fréquence d’apparition (Faible = rare, Moyen = occasionnel, Élevé = chaque jour) et son impact sur le service étudié (Faible = impact négligeable, Moyen = impact mesurable, Élevé = impact significatif). Ensuite, les gaspillages administratifs peuvent être classés comme critiques, si un ou les deux attributs correspondent au niveau Élevé.
Document(s) à télécharger
Références
- Kalbach J. 2021. Mapping Experiences: A complete guide to customer alignement through journeys, blueprints and diagrams, 2nd edition. O’Reilly, UK(en anglais)
- Regan W.J. 1963. The Service Revolution. Journal of Marketing, 27(3) (en anglais)
- Shimizu K. 1999. Le toyotisme. La Découverte, Paris