Un Service Blueprint est une représentation visuelle de tous les éléments d’un service et permet ainsi l’identification d’opportunités d’amélioration éventuelles. Idéalement, un Service Blueprint est réalisé d’une manière participative avec tous les acteurs concernés. C’est donc un outil idéal pour améliorer la coordination et synchronisation entre plusieurs services dans une organisation autour la prestation d’un service.
Table des matières
Concept
Le point de départ de chaque Service Blueprint est l’action du client, qui demande un certain service et qui déclenche différentes activités visibles ou invisibles pour le client. Liée à l’action du client sont la mesure du temps et les éléments tangibles faisant partie du service. Au niveau du fournisseur du service, il y a des actions avec ou sans contact direct avec le client et des actions. Tous ces éléments illustrés sur la figure suivante sont expliqués plus en détail dans les sections suivantes.
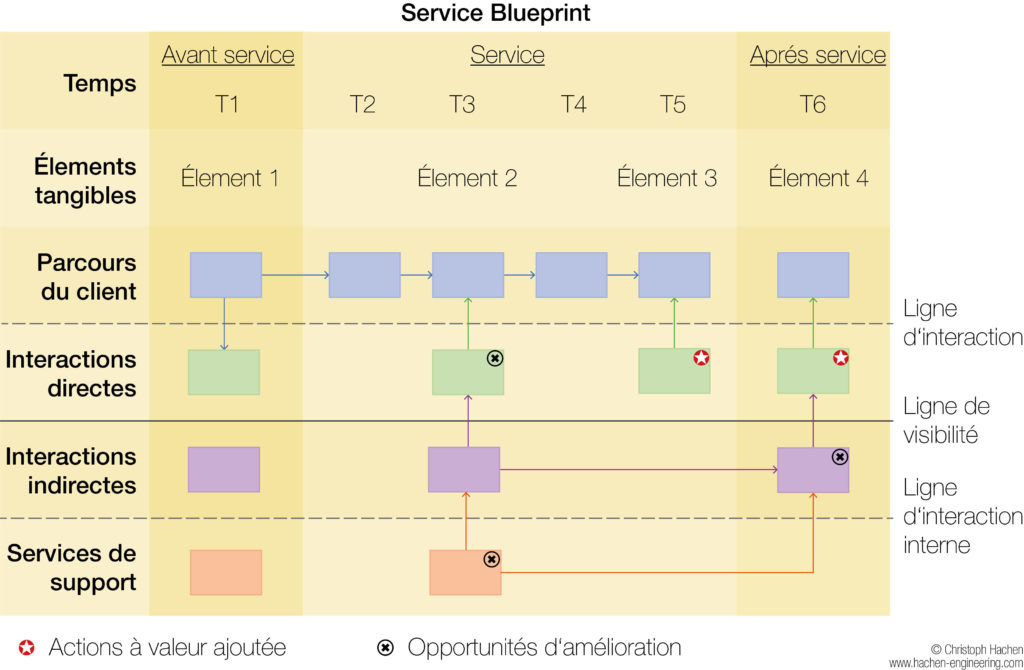
Remarque importante : Le Service Blueprint peut être comparé au Value Stream Mapping VSM (Méthode Lean), mais il est essentiel qu’un Service Blueprint ne corresponde pas à un flux de produits. Dans un Service Blueprint, l’analyse se focalise sur l’interaction entre les différentes fonctions et activités qui sont censés de fournir un service.
Parcours du client (customer journey)
Les actions du client sont le cœur du Service Blueprint car toutes les autres actions en découlent. Liées aux actions du client sont la mesure du temps écoulé et l’indication des éléments tangibles. Ces éléments peuvent être des sites web, des documents, des magasins ou d’autres objets, qui sont en rapport avec le client et le service.
Actions visibles (frontstage actions)
Les actions visibles sont les actions, qui sont en contact direct avec le client. En général, ces actions sont réalisées par une personne ou des applications (web). Ce sont des actions essentielles pour la qualité du service perçu par le client.
Actions pas visibles (backstage actions)
Les actions pas visibles sont aussi liées directement au service, mais elles ne sont pas en contact direct avec le client. Elles peuvent être déclenchées par le client même ou par les actions visibles pour le client.
Actions de support (support processes)
Les actions de support correspondent à des services, qui ne sont souvent pas liés à un service particulier. Typiquement, ce sont des services informatiques ou des services de gestion.
Processus et lignes d’interaction et de visibilité
Chaque étape du service est décrite par un processus. Dans la description d’un processus il est essentiel d’identifier les actions à valeur ajoutée. Ce sont des actions critiques, qui apportent aux clients le service recherché. Ces processus sont divisés ou groupés par la ligne d’interaction (client- actions visibles), la ligne de visibilité (actions visibles-actions pas visibles) et la ligne de visibilité interne (actions pas visibles-actions de support).
Analyse du Service Bleuprint de l’état actuel
Le but ultime d’un Service Blueprint est la définition d’actions correctives à partir de l’analyse de l’état actuel d’un service. Un bon point de départ pour réaliser cette analyse sont les gaspillages administratifs définis par l’Administration Lean. Comme expliqué dans la liste suivante, ces gaspillages sont des activités sans valeur ajoutée pour le client du service.
- Erreurs : Informations fausses, procédures et normes non suivies et oubliées ;
- Outils informatiques : Bugs informatiques, logiciels trop complexes et manque de connaissance des programmes ;
- Informations obsolètes : Catalogues obsolètes, documents pas à jour et plusieurs versions de documents ;
- Recherche d’informations : Recherche de documents, ordres incomplets, manque de communication, normes ou documents incomplets et oublis ;
- Mouvements : Déplacements entre services et postes, manque d’ergonomie et activités monotones et répétitives ;
- Organisation : Manque de formation et de polyvalence, manque de travail d’équipe et manque d’objectifs communs ;
- Attentes : Attentes d’information, attentes de décisions et changements de priorité ;
- Copies multiples : Informations papier redondantes et transcriptions manuelles d’informations entre différents supports.
Exemple d’application
L’exemple suivant illustre le Service Blueprint d’un service après-vente fictif.
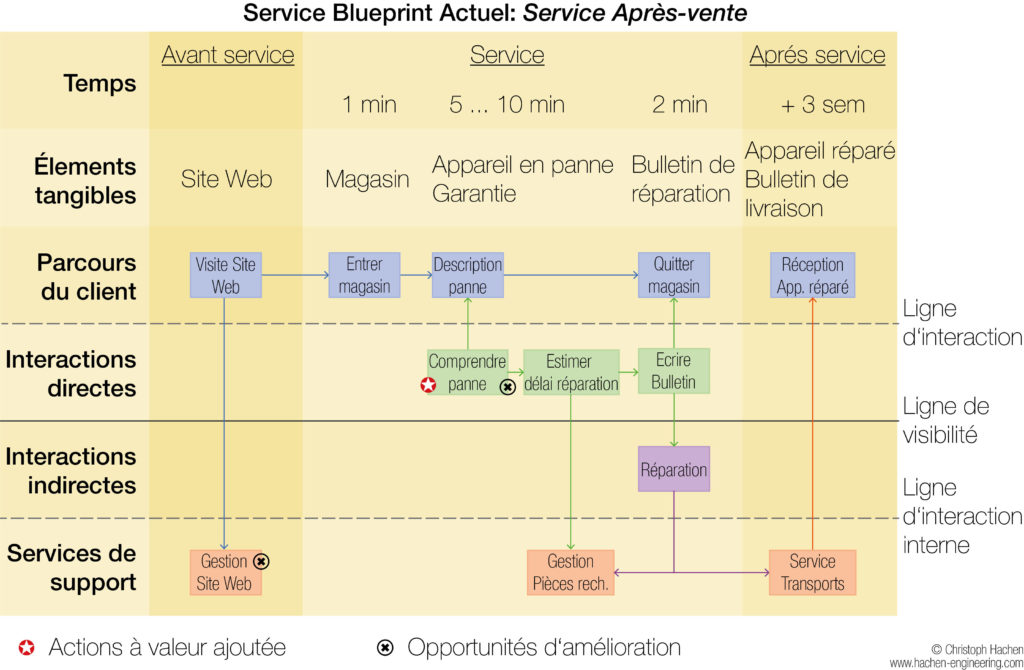
Son analyse montre deux éléments critiques. Les informations sur le site web sont insuffisantes pour donner aux clients des informations par rapport à la résolution problèmes mineurs avec le produit. Il est estimé, que 10% des cas pourraient être résolus par les clients eux-mêmes. Le deuxième élément critique est la compréhension de la panne par l’employé. Il est aussi estimé qu’un grand nombre de pannes pourraient être réparées rapidement en impliquant le service de réparation.
Un Service Blueprint amélioré est réalisé en mettant en place un site amélioré avec des informations utiles et en ajoutant l’interaction avec le service de réparation pour réaliser des réparations rapides.
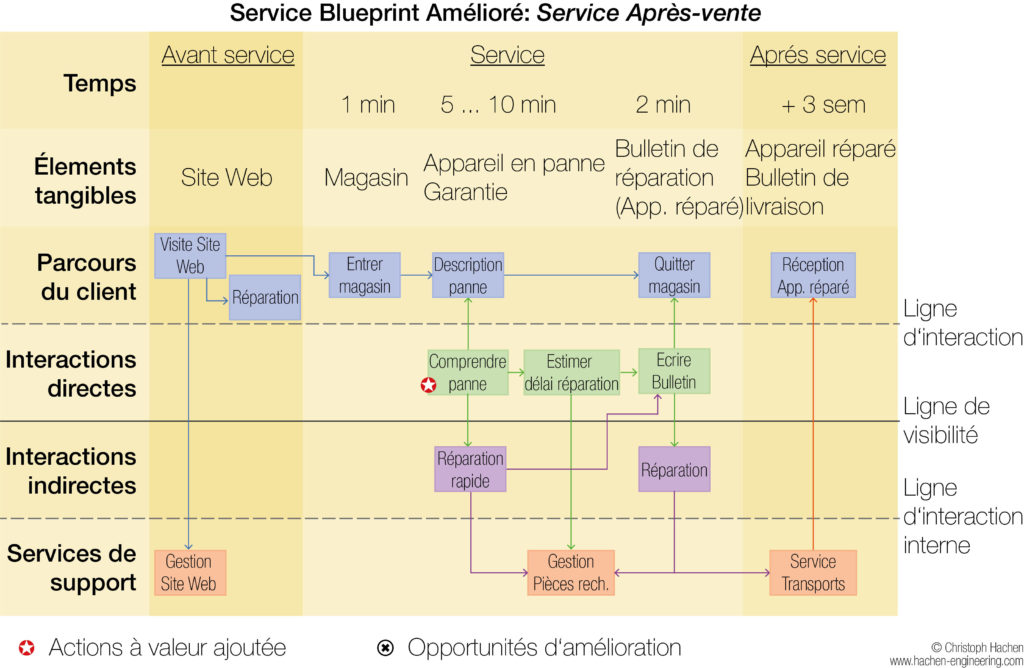
Résumé
Le Service Blueprint est une méthodologie simple et visuelle pour l’analyse structurée de services. Cette méthodologie permet d’obtenir des résultats significatifs, si elle est mise en place d’une manière interactive avec tous les acteurs impliqués.
Références
- Kalbach J. 2021. Mapping Experiences : A complete guide to customer alignement through journeys, blueprints and diagrams, 2end edition. O’Reilly, UK (en anglais)