Le Sales and Operations Planning Process S&OP est un processus de planification à long terme qui intègre tous les acteurs et fonctions importants afin de déterminer ensemble les moyens à mettre en place afin de satisfaire au mieux la demande prévisionnelle. Il s’agit d’un processus de prise de décision mensuel, qui est exécuté en général en 5 étapes. La figure suivante illustre les informations nécessaires pour réaliser ce processus.
Le processus S&OP présenté dans cet article correspond à un certain standard, mais les différents éléments peuvent varier en fonction de la typologique de l’entreprise. Cependant, le but ultime d’un tel processus est de fournir à la direction assez de données fiables sur l’évolution des opérations pour pouvoir prendre les bonnes décisions à long terme (long-term decisions).
Dans le cadre de la planification hiérarchique, le process S&OP correspond au premier niveau de planification)

Processus
Le processus S&OP est composé de 5 étapes distinctes qui sont exécutées en général une fois par mois. L’objectif de ces étapes est de construire d’une manière structurée les informations nécessaires pour les prises de décisions concernant la gestion des opérations.
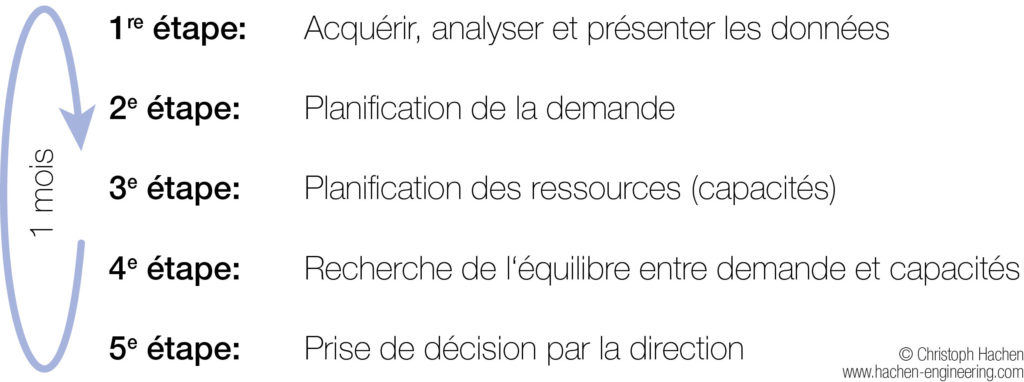
1re étape :
La première étape consiste à mettre à jour toutes les mesures logistiques (KPI). Dans le cadre du processus S&OP, il est particulièrement important de mesurer les écarts entre les plans et le réalisé (production, approvisionnement, prévisions de vente, investissements, etc.).
2e étape :
La deuxième étape consiste à consolider la demande actuelle et future. Les différents éléments à mettre à jour sont 1) les écarts importants entre prévisions et ventes réalisées, 2) le lancement de nouveaux produits, 3) l’annulation de produits existants, 4) des promotions et 5) les prévisions. Un point critique est également la mise à jour des priorités par rapport à des marchés ou des clients stratégiques, et par rapports aux retards de livraison éventuels.
3e étape :
La troisième étape consiste à la planification des capacités de production et de l’approvisionnement. Pour limiter la complexité de la tâche, il est indispensable de se focaliser seulement sur les ressources critiques (goulets d’étranglement et fournisseurs), qui limitent la capacité globale de l’entreprise à répondre à la demande.
4e étape :
La quatrième étape consiste à identifier les écarts critiques entre la demande et les capacités planifiées (production et approvisionnement). Ces écarts importants seront transmis à la direction pour la cinquième étape, s’ils ne peuvent pas être absorbées par un ajustement des plans.
5e étape :
La dernière étape du processus est consacrée à l’analyse des mesures de performance (KPI) et à l’analyse des écarts critiques entre les plans et les capacités et l’approvisionnement à disposition. Ces informations doivent donner assez d’informations à la direction pour qu’elle puisse décider les actions correctives adéquates.
Le processus S&OP constitue la base pour l’étape de réalisation de plans directeurs de production PDP (planification hiérarchique, deuxième niveau de planification).
Résumé
Le processus S&OP est essentiel pour pouvoir répondre à la demande d’une manière économique. C’est un processus simple, mais sa mise en place ne l’est pas. Voici les éléments les plus critiques de ce processus :
- Une collaboration étroite entre les différentes fonctions de l’entreprise (production, vente, développement, finance, etc.) ;
- La disponibilité de nombreuses mesures de performance (production, ventes, achats, etc.), qui permettent d’identifier les écarts entre les plans et le réalisé ;
- La mesure de la fiabilité des prévisions de vente.
Mais comme il n’existe en principe pas d’alternatives à un tel processus, il est indispensable d’accepter que le processus S&OP parfait n’existe pas. Il devrait donc être inscrit dans une démarche d’amélioration continue pour pouvoir être adapté en continue aux évolutions des exigences.
Matériel supplémentaire
Résumé du processus S&OP (en anglais): PDF
Références
- Dougherty J. et C. Gray. 2006. Sales & Operations Planning – Best Practices. Partners for Excellence, Belmont (en anglais)
- Sheldon, D. H. 2006. World class sales and operations planning: a guide to successful implementation and robust execution. J. Ross Publishing, Ft. Lauderdale (en anglais)