L’avantage des ERP modernes est qu’il n’existe en principe pas de limite de nombre et de complexité des produits gérés. Dans un marché, qui demande des produits de plus en plus complexes avec des durées de vie de plus en plus courtes (the new normal), il est fréquent de retrouver des systèmes qui doivent gérer plus que 10’000 articles (produits finis, sous-ensembles, matière première, etc.). Si on compte pour chaque article au moins trois à cinq variables de gestion à définir (tailles de lot, stocks de sécurité, stratégie de production, etc.), on obtient facilement un nombre de plus de 50’000 paramètres de gestion à gérer et à optimiser. En fonction de la variabilité de l’environnement de production et des ressources à disposition, cette tâche peut s’avérer très difficile à réaliser.
L’idée de base du concept de la configuration ABC est de fournir des règles, qui permettent de définir à partir de la classification multicritères ABC une configuration « optimale » des paramètres de gestion (ordre de grandeur).
Concept
Le concept de la configuration ABC est basé sur la classification multicritères ABC, qui permet de classifier chaque article en fonction de plusieurs critères comme le niveau et la régularité de la demande, le cycle de vie du produit et la typologie du produit. En fonction de l’environnement de production, d’autres critères peuvent être ajoutés comme la complexité des opérations ou la durée de conservation maximale. Il est encore à noter qu’une classification multicritère ABC peut être composée de classifications quantitatives (mesure du volume et de la variabilité) comme de mesures qualitatives (cycle de vie). A partir de la classification multicritère ABC de chaque article, des règles sont définies pour les paramètres de gestion taille de lot, stock de sécurité et mode de gestion des flux. Les valeurs obtenues ainsi ne correspondent pas forcément à des valeurs optimales (d’un point de vue mathématique), mais plutôt à des ordres de grandeurs corrects.
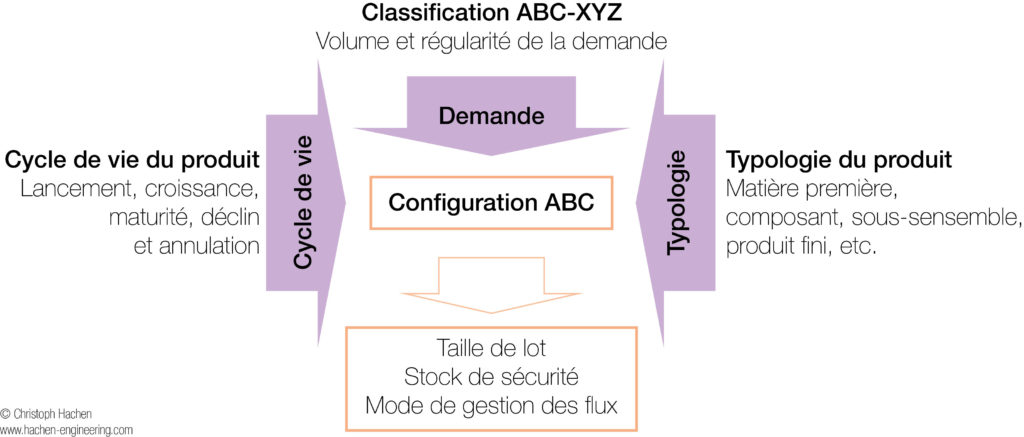
Classification ABC-XYZ
La classification ABC-XYZ est essentielle pour déterminer le volume et la régularité de la demande. Elle est basée sur la classification ABC (analyse Pareto) et la mesure de la régularité de la demande à l’aide du coefficient de la régularité CV (= écart-type/moyenne de la demande). Pour la classification ABC, les valeurs typiques pour les volumes cumulées sont de 80% (classe A), 15% (classe B) et 5% (classe C). Pour la mesure de la variabilité de la demande, les valeurs typiques pour le coefficient de variabilité CV sont de < 0.8 (classe X), 0.8 … 1.2 (classe Y) et > 1.2 (classe Z). La mesure du CV est en générale basé sur les ventes ou consommations mensuelles des derniers 6 à 12 mois.
A partir de la classification ABC-XYZ, des règles sont définies pour les tailles de lot, le stock de sécurité et le choix du mode de gestion des flux. La taille de lot et le stock de sécurité sont calculés à partir de la demande moyenne pendent le délai de réapprovisionnement DMR. Dans un scénario idéal (demande et délai de réapprovisionnement stables), la taille de lot correspond exactement à la valeur de DMR. Il est maintenant possible de définir les formules suivantes pour la taille de lot et le stock de sécurité :
Taille de lot = fvar x DMR
Stock de sécurité = fsec x DMR avec (niveau moyen):
Classe XYZ | X | Y | Z |
---|---|---|---|
fvar (moyen) | 1.5 | 3 | 6 |
Classe ABC | A | B | C |
---|---|---|---|
fsec (moyen) | 1.0 | 0.5 | 0.2 |
Les livraisons des articles A sont donc sécurisées à l’aide de stocks de sécurité plus élevées, et l’absorption des pics de demande est assuré pour les articles Z via des tailles de los plus élevées. Les valeurs choisies pour fvar et fsec sont des estimations de base, qui peuvent varier en fonction de l’environnement de production, et de la typologie de produit.
Concernant le choix du mode de gestion des flux, le flux tiré et la production répétitive sont conseillés pour des articles avec une demande stable (articles X).
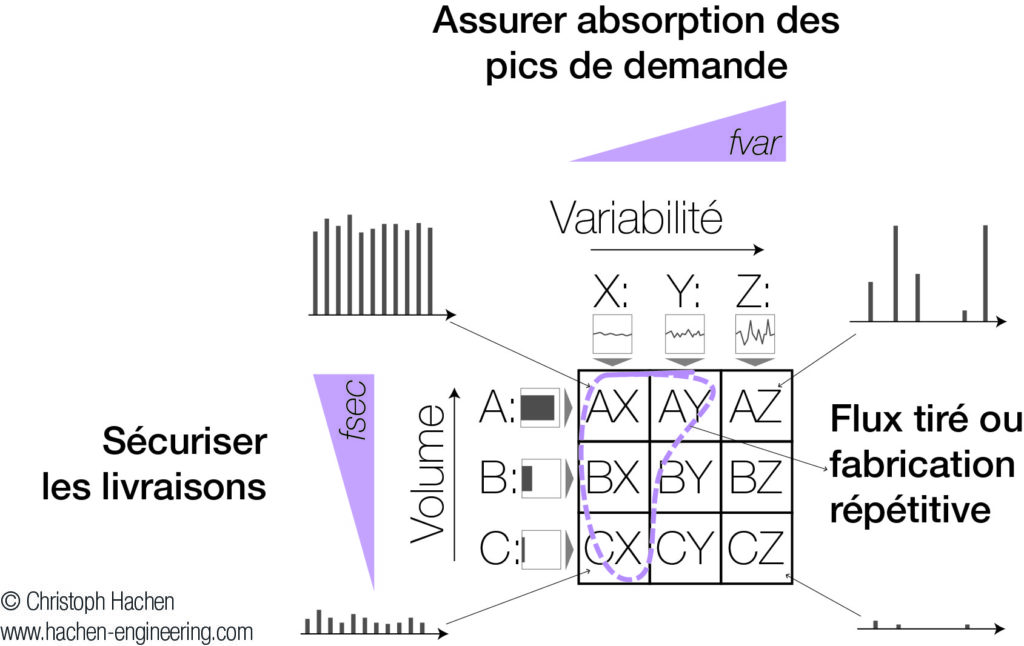
Cycle de vie de produits
Le cycle de vie de produits a un impact significatif sur le choix des paramètres de gestion surtout au début et à la fin du cycle de vie. Au début du cycle de vie de produits il est en général essentiel d’assurer leurs disponibilités pour la campagne de lancement du nouveau produit (Lancement à Croissance). Le choix typique pour ce stade est la fabrication sur stock et l’établissement d’un certain niveau de sécurité. A la fin du cycle de vie de produits, il est en général important d’éviter le risque d’obsolescence (Déclin à Annulation). Le choix typique est la fabrication à la commande et la mise à zéro des stocks de sécurité éventuels. Pendent le cycle de vie Maturité, le choix des paramètres de gestion est fait en fonction de la classification ABC-XYZ.
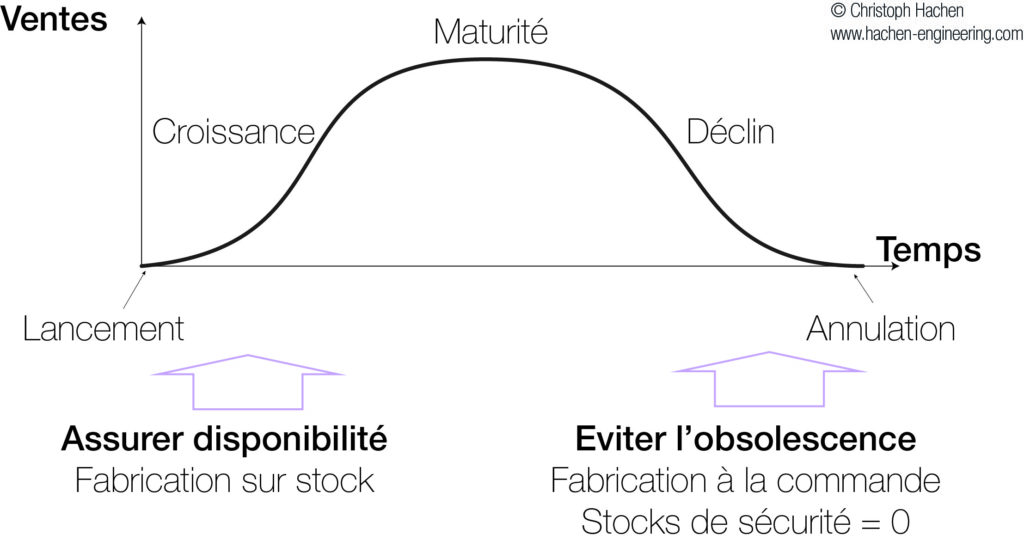
Typologie des produits
L’emplacement des stocks (de sécurité) dans la chaîne logistique dépend de plusieurs facteurs comme la stratégie de production choisie, la criticité d’un composant et/ou la fiabilité d’un processus. Cependant d’un point de vue général, il est souvent préférable d’avoir des stocks (de sécurité) plutôt au niveau de la matière première qu’au niveau de produits finis. Un manque de disponibilité au niveau de la matière première (ou composants de base) peut stopper l’ensemble des opérations, tandis qu’une rupture au niveau des produits finis peut correspondre juste à une interruption momentanée des livraisons.
Pour l’approvisionnement de la matière première, un plus haut niveau des paramètres fvar et fsec peut être choisi que pour la fabrication des produits finis. Les tabelles suivantes montrent des choix possibles pour les paramètres fvar et fsec (niveaux faible et élevé).5
Classe XYZ | X | Y | Z |
---|---|---|---|
fvar (moyen) | 1.2 | 2.0 | 4.0 |
Classe ABC | A | B | C |
---|---|---|---|
fsec (moyen) | 0.5 | 0.2 | 0.0 |
Classe XYZ | X | Y | Z |
---|---|---|---|
fvar (élevé) | 1.5 | 3.0 | 6.0 |
Classe ABC | B | C | |
---|---|---|---|
fsec (élevé) | 1.5 | 1.0 | 0.5 |
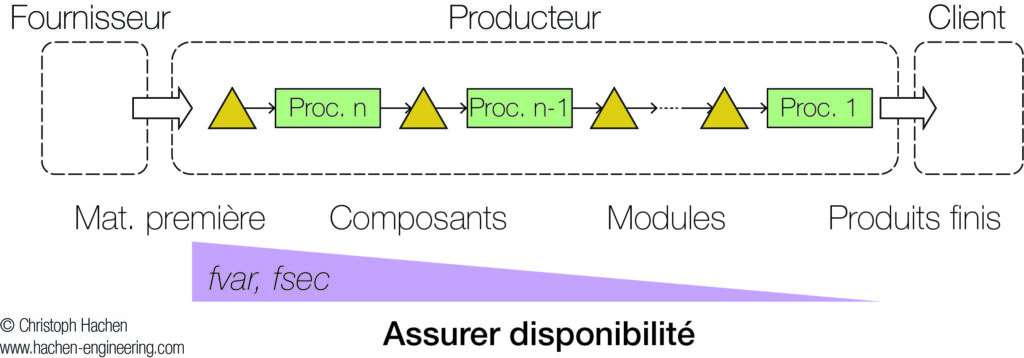
Application
La tabelle suivante montre un exemple typique pour le choix des variables en fonction du cycle de vie de produits et la typologie du produit :
Typologie | Cycle de vie: Croissance | Cycle de vie: Maturité | Cycle de vie: Déclin |
---|---|---|---|
Matière première | Fabrication sur stock, selon plan de lancement de productionj | Classification ABC-XYZ, fvar et fsec élevés | Fabrication à la commande, stocks de sécurité = 0 |
Sous-assemblages | Classification ABC-XYZ, fvar et fsec moyens | ||
Produits finis | Classification ABC-XYZ, fvar et fsec faibles |
A partir du calcul des paramètres de gestion « optimale », il est ensuite possible de juger la criticité via des ratios entre les valeurs actuelles et optimales. Pour identifier les articles les plus critiques, il est conseillé de trier les ratios les plus élevés en fonction de la couverture du stock (trop élevée ou trop faible).
Résumé
La configuration ABC est un outil d’aide à la décision, qui permet de vérifier le paramétrage d’un grand nombre d’articles. Il permet d’identifier rapidement des articles critiques avec des couvertures de stock trop élevées ou trop faibles (manque de disponibilité fréquente) à cause de tailles de lot et/ou stocks de sécurité trop élevées ou trop faibles. La configuration ABC permet également d’identifier les articles, qui peuvent être gérés avec la méthode Kanban (flux tiré) et/ou via une production répétitive (grands volumes de production de produits standards, selon un programme de production cadencé).